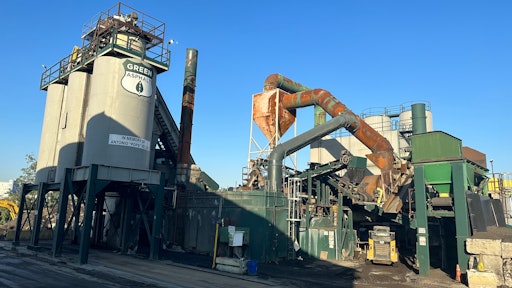
In the middle of 2016, Green Asphalt was still trying to define its identity as a company, and how they wanted to project themselves into an industry that, at the time, wasn't interested in what they had to say. More troubling, however, no one was interested in what they were making.
"We made an innovative product that no one wanted," Jim McMurray told me, as we started a full tour of their facilities in Queens, New York. He's the VP general manager of Green Asphalt, the kind of person who's so passionate about reclaimed asphalt pavement (RAP) that, at one point in the tour, he thrust his hand into a large pile of newly crushed material and held it up for me to see.
Needless to say, from the minute I set foot on the premises, there was an energy that, at first, I couldn't put my finger on, but eventually became clear when I saw this quote on the side of one of their aggregate loading bins, "Be humble and kick ass."Jim McMurray standing in front of his pile of "black sand"Brandon Noel
McMurray was visibly sentimental when explaining the origin of the slogan.
About five years prior, in Green Asphalt's very early days, the CEO, Michael Capasso, challenged his leadership through a series of corporate coaching sessions. They were all tasked with picking one person from the entire company with whom they would want travel to the moon. The concept is a fairly typical corporate exercise, but McMurray and the company's owner happened to select the exact same person. That was one of their mechanics, Brian Cranston, who sadly passed away in 2019.
"We had to explain why we chose that person, explaining all their characteristics," McMurray said. "That's where we came up with that motto. It means a lot to the company."
An Example of True Disruption
There's a lot of talk in the corporate world about disruption. Disruption of supply chains, of product offerings, of marketplaces, and on-and-on, especially when it comes to the technology industry. What does real disruption really look like? At its most basic disruption means changing the rules of competition in an industry by doing things differently.
In a practical sense, disruption identifies areas of consumer or market demand, and then applies new techniques, platforms, or paradigms in order to do what is already being done at a lower cost. Disruption like this takes action, and often garners significant investment, because of the potential for profit. In this case, it looks like a company that absorbed a whole lot of risk on an innovative idea where no tangible demand for it existed.
"In January of 2008, before Green Asphalt existed, the price of asphalt cement (AC) was around $400," McMurray said. "Then, by August of that year, it was almost $960." But this was just one of the factors that started to align the need for disruption in the asphalt market.
Due to solid waste regulations in New York City, as well as a general lack of available real estate, companies have to pay to dump their RAP. Around the same time, the price to dump went from a reasonable $15-$20 per ton all the way up to $60-$70 virtually overnight. In the wake of this one-two-punch, a well-known scientist approached the company with a potential solution that involved a process for producing high-performance asphalt mixes from 100% RAP.
Currently, they have a contract with the city DOT to take their millings in, because they simply don’t have enough space to put them anywhere else, and through that, they are able to offer an all-in-one solution where they dispose of their millings and pick up recycled asphalt.
"We were like, 'yeah, let's make let's make 100% recycled asphalt,' of course, none of us really ever made asphalt before," McMurray explained. "We started figuring out how to permit a plant like this. The original plant in 2011 was a Frankenstein, hodgepodge of different manufacturers, and then our patented baghouse. Then we worked backwards from the New York City mixes, and basically reverse engineered it using only the materials we had."
Open Ended Experimentation
The process of development has been anything but a straight line. For example, Green Asphalt currently utilizes a paraffin oil based rejuvenator, but they've literally tried everything that you can imagine. Nothing was off the table.
"In our first experiments, we used waste motor oil, and we even tried French fry oil," McMurray said. Incredibly, that didn't stick. "The reason we switched was not necessarily because of performance. It was because the New York City DOT did not have waste motor oil on their approved rejuvenator list. Currently we have mixes at six different labs and they're running tests as we're trying to find the best rejuvenator."
EPDs and Beyond
Green Asphalt has four published environmental product declarations (EPD) created with the National Asphalt Association's (NAPA) Emerald Eco Label tool. Two of them are for 100% RAP mix designs. Their A1 and A2 scores are near zero, both showing an A1(.78) and A2(.11), which helps keep their overall Global Warming Potential (GWP) low at 43.91. All published EPDs are available on NAPA's website: https://asphaltepd.org
Green Asphalt did spend a significant amount of time and research ensuring that beneath the coating of asphalt, the gradation of the underlying stone was correct after the screening process. This marks the biggest departure between how they treat RAP versus the majority. In plants where 20% RAP content is still the norm, it's only treated as a single type of aggregate, but the no-additional AC was the real goal.
Recycled Asphalt Alchemy?
On the surface of things, the operations at Green Asphalt have the appearance of a regular run-of-the-mill asphalt plant. It's important to note this, because one of the most reiterated things during my day at the plant was the fact that ANY asphalt plant can be converted into a 100% RAP producing plant, batch or continuous. The existing machinery is all the same, the only exception being the additional, patented baghouse. Largely, it isn't what they do that is so different, as much as it is, how they do things differently.
The whole process of conversion only takes about three weeks. That's something that could be accomplished during any normal offseason. Shutdown in Q4 and reopen for business in Q1 with the ability to produce a mix at a lower cost, and a higher margin. But what if your asphalt plant has its own quarry associated with it?
"A quarry is a limited resource," said McMurray. "What's the plan when it runs out? In California, they're no longer permitting new quarries. What if you could keep that resource in the ground? Instead of selling it to yourself at a discount, you could sell it to someone else for a profit?"
The whole process begins with an enormous, unprocessed pile of RAP. A sight surely familiar to anyone working in asphalt production. The RAP is then fed into a standard impact crusher, fitted with a magnetic filtering system to capture any incidental metals. From there it's processed by way of "fractionating" into three different byproducts simultaneously: what Green Asphalt calls "black sand", then 3/8, and 3/4 aggregates. From these and their rejuvenator alone, they are able to reproduce every mix that New York City utilizes. No additional AC is used.
McMurray grabbed big double handful of the black sand and held it up to me. "This is all coated in asphalt," he said. "This has 6% to 6.5% asphalt content. This is like black gold. To make top course you would use approximately 50% black sand and 50% of the 3/8 RAP aggregate."
Conventionally, at least 5% of your mix is going to contain fresh AC, the price of which is volatile. It's fluctuations mean a highly fluctuating price of asphalt per ton. For Green Asphalt, they are incorporating only .5% of rejuvenator, the price of which is fairly stable. Green Asphalt has been charging $58 per ton steadily for its 100% RAP mixes, steadily for 15 years.
Some local city contractors who use it, factor that stability so greatly into their bids, that they will delay a project if they have to wait to get Green Asphalt. This very loyal customer base continues to grow, because the product offers emissions reductions and cost savings, but the growth is challenged by government agencies.
"Besides the rejuvenator, we didn't want to have to add AC," McMurray emphasized. "That would defeat the purpose, Right? There's so much it's coated on there. Why not reuse it? Why have these piles all over the country? Most asphalt plants make one product. Those using 15%, 20%, and 30% RAP, are using these combined, they crushed it down into one size, and inject it into their mix. They're not doing the specific quality control you see here."
McMurray continued to explain that this previous way of processing RAP contributed to some of the misconceptions about it. "Historically, it was crushed but it wasn't tested, and then it just put back in the mix. It's why there's been a misconception that RAP is bad. The stockpiles weren't tested properly, they weren't sent out for asphalt extractions. That's why, in the past, when someone tried to go up to 30%-40% RAP the mixes failed."
Essentially, it's apples-and-oranges. To grasp what Green Asphalt is doing, you can't think of the RAP in the same way. "The previous way the industry has treated RAP is an outdated process. It's based on outdated data," McMurray said, almost breathlessly.
So, the question is, with the focus on sustainability, reducing emissions, and greener more environmentally viable solutions, like those being heavily supported by federal policy and funding, why isn't this the norm? Obviously, the regulations regarding performance and mix design limit the amount of RAP, but how do you get new data in front of the people that have the authority to update those regulations?
For Green Asphalt's team, these questions have been much harder than the science behind making 100% recycled asphalt work.
A Radical RAP Paradigm Shift
From talking with McMurray and the Green Asphalt team, you realize that when they talk about RAP and what is generically considered RAP, they are dramatically different things. They believe that when previous failed studies were conducted, likely using between 20%-30% RAP content in the mix, the problem was specifically in how the RAP was treated. However, the science behind RAP has changed.
They argue that municipal, state, and federal regulation hasn't kept pace with the evolution of RAP science, despite the growing political support for greener, more sustainable solutions. Meanwhile, other industries rush to put everything from waste rubber from tires, recycled single-use plastic material, and, as in the state of Florida, radioactive byproducts into our asphalt mixes!
"This is not a waste product that you're trying to jam into your mix, and make it work," McMurray said poignantly. "It is our mix. It is our raw material. It was made by an approved plant, with approved aggregate, and approved oil. It's all sitting in the millings. So, bring it back to life and turn it back in."
Green Asphalt has done several presentations at various events, both within the industry and for various people who hold public office. The response is always positive, especially when they explain that it costs 30% less than conventional asphalt mixes.
"We tell the town officials, the elected officials, and they say, 'Wow, this is great. I'm gonna go talk to my DOT managers,'" McMurray told me. "Then they come back and say, 'It can't be done 100% RAP, it's no good. You can't do that,' and just it just dies on the fire."
This, despite the fact that they have, and can demonstrate the mix's consistent performance capabilities. All too often, the issue is that they are unable to get an audience with the officials, or, are frequently ghosted or stonewalled when they ask for simple things like: what are the exact requirements they need to prove they can meet in order to be approved.
"Agencies across the country have talked about moving towards a balanced mix design, and in that there are two main factors: rutting and cracking," McMurray explained. "If you find that balance between rutting and cracking, you have a mix that lasts a long time, it's sustainable. A balanced mix design has certain criteria, rutting tests and a cracking test. If you meet those, you've made your asphalt. What we want to know is: what is that criteria? The goal should be to simplify, to make it very clear and attainable so that you can allow for innovation, not just for our experimentation, but for others to experiment."
The Making of True Believers
Part of the problem is that every DOT, city to state to federal, there can be different variables. Everyone wants or needs slightly different things, but even if they are the same, whenever you initiate the process with a new DOT you have to start from scratch. Prove the same things over again. That can be a lot to consider for a producer, even if you are very interested in doing a conversion on your plant. Where do you start?
"That's a great question," said Kerianne Melillo, chief marketing officer at Green Asphalt. "That's something we bring to the table along with the plant conversion, essentially, a consulting service to share with other producers what we've learned through the process over the last ten years. We want to be part of the solution, getting this through a city agency or a state agency. What tests do you have to have done? We have a lot of that information already. We've done the research, we've been through the trials and tribulations."
She continued, "Once you have a meeting with a DOT, you have to be prepared to answer their questions, and their questions are unequivocally engineering based, they are almost never questioning the sustainability benefits of it. It's very rarely a question of if there's a cost benefit. It's really focused on does it perform. So, we have been through that barrier already and we know how to approach those types of hurdles."
On one occasion, they invited a city DOT to a project on a stretch of Pelham Parkway that was being repaved with their 100% mix. "They were very skeptical," Melillo said. "They turned to me, and they said, 'How can I trust that this is 100% recycled, because this looks like it couldn't be more than 20,' and I asked if they would you like to drive to the plant, because we're making it right now. They were blown away by how it looked, how it smelled, how it was paved out. They were blown away to the point where they didn't actually believe it was 100% recycled."
"We have the ability to meet whatever performance is requested," McMurray said. "Part of our confusion is that balanced mix design, performance based specifications, are not widely accepted. No one can give us that list. So, we don't even know what we're trying to meet. They want performance data, and we don't know what they're comparing it to."
Melillo interjected, "When it comes to conventional asphalt producers, they're meeting the volumetric specifications, which we can also meet. But our confusion comes when we speak with someone from a DOT who wants to see our performance data. After we give it to them their response might be that it isn't good enough, but compared to what? We don't have any basis for what they want, and whatever that might be, we'll find a way to get there."
The Net-Zero End Point
Something that you have to consider is where the industry says it is headed. Many major players have signed on to the goal of a net-zero carbon emission future by 2050. Everyone I have spoken to agrees that higher RAP percentages will have to, at least, be a functional part of how we attain that goal.
The Inflation Reduction Act has provisions to offset the costs of plant upgrades that result in the production of materials with a lower embodied carbon. That could help a producer make the necessary changes, while still offering conventional mixes at the same time. Green Asphalt currently offers traditional mixes, something they added to their offerings, almost to just prove that they could do both.
Additionally, according the Green Asphalt, after undergoing a plant conversion to be able to produce the 100% RAP mix, it can pay for initial investment in as little as six months.
"We did it not knowing if we would sell anything," McMurray said. "The city in New York didn't accept 100% RAP mixes when we started doing this. Now, everyone's waiting for the customers ask for it. We believed in providing it first, and then get the customers to change their mind. Someone's got to have the guts to just do it."