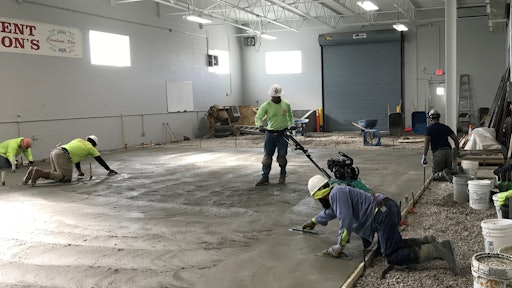
Of the handful of issues contractors have to contend with, one of the most difficult has been the need to discover skilled labor. It's a rare story now to find a new hire with no experience willing to stick through the years and become that indispensable skilled worker you needed last week. The Operative Plasterers' & Cement Masons' International Association (OPCMIA) recognizes this and with about 55 different apprenticeship programs spread out over the country, they provide training programs that specialize in the training needed. Staring back in 1864, making it one of the oldest unions in the U.S., the OPCMIA's current membership is about 48,000 including journeymen.
The local union/JATC conducts joint apprenticeship training programs through collective bargaining agreements (CBA) and standards. The JATC partners with construction companies in the CBA and through the apprenticeship program helps deliver training for the future workforce.
"We have different apprenticeship programs established throughout the country," says Nick Demonte, OPCMIA-ITF Cement Mason Coordinator, and master trainer through CPWR. "It's a great opportunity to come into training, where you might not know anything about concrete or plastering work." The key is those training in the apprenticeship program are also earning a good wage and are becoming more valuable to the contractor.
Demonte has almost 30 years of experience in construction and has been instructing now for 11 years. He started in Cleveland, Ohio as the instructor for the local 404. After being promoted to the international level, the OPCMIA started its International Training Fund (ITF) to help all the locals across the country – assisting them in any way they can. Recently, Demonte has been promoted to coordinator and has his eyes set on the instructors.
“My goal is to train the instructors. To make sure they can go to their respective locals with the best knowledge available and train the apprentices and journeymen,” he says. His goal is aimed at one massive question: what needs to happen to train instructors, so they have the skills to train apprentices and journeymen in the future workforce.
They want to accredit all their instructors and all their apprentices and journeymen to receive as many certifications as possible.
“Education is power, and it can lead to more money,” he says. “It’s something that nobody can every take away from you – that’s why we’ve partnered with the American Society of Concrete Contractors (ASCC) and the American Concrete Institute (ACI).”
Earn While You Learn
Regulated through the Department of Labor, pay is based on hours from both on-the-job training and classroom-related instruction- earning a raise after completing the required hours. These can be accomplished in yearly increments, while some programs are scheduled for a six-month increment.
Training by the OPCMIA works within a working relationship with signatory contractors. “When I was the instructor,” explains Demonte, “we had people that were looking for work. We brought them through our apprenticeship program, and then we placed them with a signatory contractor. We gave them basic skills to go on the jobsite."
Weather can be an issue for construction in general and it’s no different for training. For Demonte, in Cleveland, they conducted their training during the winter, starting in December. The month started with first-year apprentices, 8 hours a day, 40 hours a week. Second-year apprentices are brought in the second week. Third year on the third week. "The national standard is 144 hours, but the 404 provided 160 hours of training of 4 weeks of 40 per week," says Demonte. Classes are scheduled ahead of time and provided to contractors to aid in scheduling.
"We try to give [the apprentices] the skills that maybe the contractor doesn't have enough time on the job to teach him all aspects of our trade," he adds.
The apprenticeship uses a specific curriculum designed for first-, second- and third-years with learning activities from instructors to apprentices and journeymen – they even provide virtual classrooms. Examples of topics are polishing, blueprint reading, form setting, history of concrete, safety, and many others.
There will be a morning classroom with hands-on training afterward to practice proper methods. For form setting, for example, they’ll gain the experience in using wood and metal in various sizes allowing them to be familiar with the different applications. “Whether you’re pouring a sidewalk, the pavement in an airport, doing walls, doing foundations, all those different aspects are incorporated in our curriculum,” adds Demonte. Basic skills and aspects are also included – skills like math conversions, accurately taking and reading a tape measure, how to tie a straight line, how to put a pin plumb, etc.
Instructors have the flexibility to create a different learning path for the structure of a program. In Cleveland, Demonte’s program included a project at the end of the year. While teaching a garage slab for first-year apprentices, he taught all the skills you would need to plan, set up and work a garage slab on their own – even down to drawing the blueprint. Training becomes more advanced as the program progresses.
Aside from the core “old school” skills, OPCMIA have also incorporated robotic total stations as well as other new innovative solutions coming out in the construction industry. Training can also include decorative, polishing concrete, overlays, as well as drug and alcohol awareness, mental health, and suicide prevention.
“What separates us from the non-union sector is the training that's provided,” says Demonte. In a non-union situation or with a contractor that might not be involved with a union, all the training would be taught on the jobsite.
Visit your local office and connect with one of the association’s business managers and/or business agents to get the conversation going. There are different ways to sign up and start working. Signatory contractors would be able to call and request a handful of workers for a job. Provided they also take on some apprentices based on how many workers needed, the office will be able to help. Search online at OPCMIA.org to help find your local OPCMIA office.
Demonte sees it like an investment where both contractor and union are invested in the development of what could be a future leader in the industry. “The end goal is for you to make money along with the contractor,” he says. “That’s always the end goal.”